Lantian Precision Casting Factory--Polishing details with craftsmanship, defining precision with technology.
Stainless steel lost wax casting (investment casting) is a high-end technology of pouring metal liquid after wax molding and dewaxing at high temperature, which is widely used in aerospace, medical equipment, automotive parts and other fields with strict requirements on precision and performance. The core process includes the following key links:
1.Wax mold design and production
Combined with professional modeling technology or manual wax carving process, the complex structure of the customer's design drawings is accurately restored, and the size error of the wax mold is strictly controlled within ±0.15mm. Through sand blasting, cleaning and other pre-treatment processes, the surface of the wax mold is smooth and free of defects, providing an ideal substrate for subsequent shell making.
2.Ceramic slurry shell making
Wax molds are assembled into modules using the “tree planting” process, and then dipped and coated with high-temperature resistant ceramic slurry layer by layer (alternating fine and coarse slurry) to form ceramic shell molds of uniform thickness. The whole process is done in a constant temperature workshop, which ensures the fluidity of the paste and the stability of curing, and provides reliable support for high temperature casting.
3.Dewaxing and baking
The ceramic shell mold is heated up to 1200°C to completely vaporize the wax and form a hollow cavity. After roasting, the strength of the mold is significantly increased and the residual volatiles are removed to ensure that no impurities interfere with the molten steel pouring process.
4.Steel pouring and molding
A vacuum induction furnace is used to melt stainless steel, precisely controlling the pouring temperature and speed to avoid defects such as porosity and shrinkage. After cooling, high precision blanks are obtained through the post-treatment processes of shell shaking, shot blasting and sand cleaning.
5.Post-processing and Inspection
After CNC finishing, grinding and other processes, the blank parts are processed to achieve IT6-IT8 grade precision, with surface roughness Ra≤0.8μm. The whole process is inspected by CMM, spectral analyzer and other equipments to ensure that it meets the international quality standards.
Core advantages of the process:
Complex structure one-time molding: it can cast thin-walled (≥0.5mm), staggered internal cavities and other parts that are difficult to realize by traditional processes, reducing the cost of subsequent processing.
High consistency: the size deviation of mass-produced parts is ≤0.15mm, the machining allowance is reduced by 30%-50%, which significantly improves the material utilization rate.
Flexible surface treatment: support sandblasting, mirror polishing, PVD coating and other customized surface treatment to meet diversified application requirements.
Core competitiveness of professional precision casting factory
As a technology-driven enterprise that has been deeply engaged in the field of precision casting for many years, we provide customers with one-stop solutions from design to delivery by taking innovative processes and full-process services as the core.
1.Advanced equipment and technology precipitation
The introduction of automated shell production line and high-precision ceramic paste spraying system supports 24-hour continuous production with industry-leading yield rate.
Equipped with microscopes, spectral analyzers and other professional testing equipment, we monitor the quality from the melting of materials to the delivery of finished products.
2.Rigorous quality control and standardized management
Through IATF16949 automotive industry certification, we have established 12 quality inspection processes, from the first wax mold inspection to the finished product inspection, to ensure zero-defect delivery.
Each batch of products comes with a complete material report and dimensional inspection records, making the data transparent and traceable.
3.Flexible production and quick response
Short sampling period for standard parts and rapid delivery of complex customized parts help customers accelerate the R&D process.
With an annual production capacity of over 5,000 tons, we can flexibly respond to the demands of small-lot trial production and large-scale orders, taking into account both efficiency and cost control.
4.Customized casting services and industry experience
We provide professional modeling, mold design and process optimization technical support to help customers shorten the product launch cycle.
We have accumulated a wealth of case studies in medical devices, automotive parts and other fields, and have successfully served high-end laboratories, research institutions and global supply chain enterprises.
Contact us now to get a customized solution!
Whether you need high-precision gears, high-temperature-resistant valves, or customized industrial parts, we will provide reliable protection for your projects with our precision casting technology and efficient services.
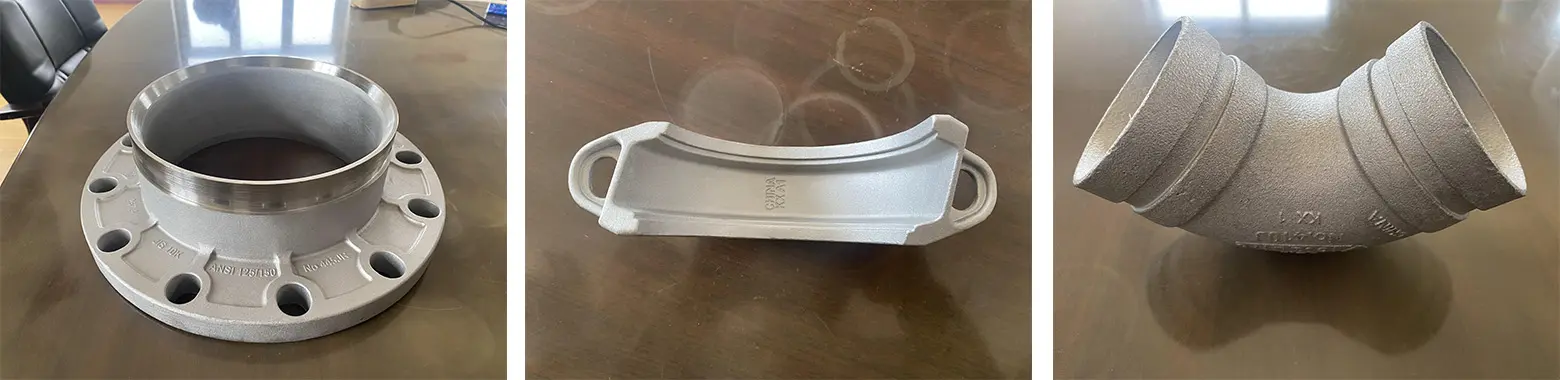
Action Channel:
Choose a partner, choose a trusted precision casting expert!
--Enabling manufacturing with technology, winning the future with quality.